在半導體制造的封裝測試環節,溫度控制的精度與穩定性直接影響芯片的可靠性、性能及成品率。半導體深冷機(Chiller)作為核心溫控設備,通過高精度、多場景的溫控能力,為封裝測試工藝提供了關鍵保障。
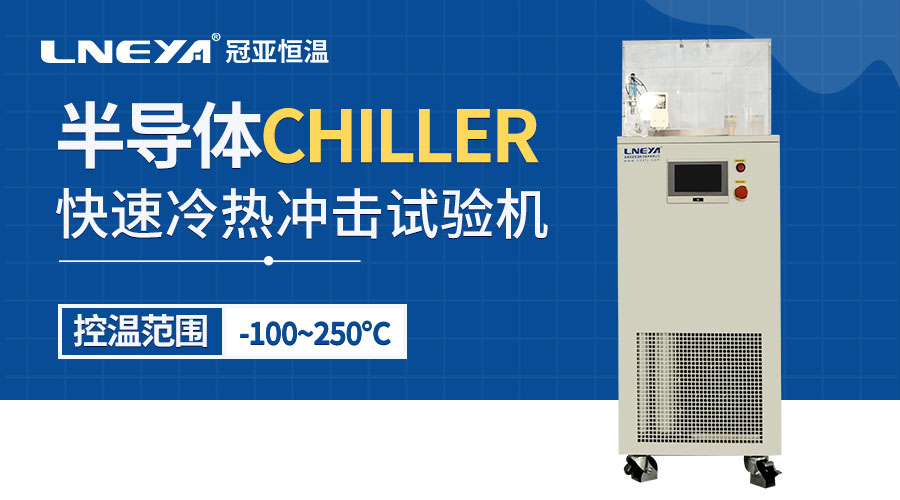
一、技術原理:高精度溫控與動態響應能力
(一)帕爾帖效應與熱電轉換
半導體深冷機基于帕爾帖效應實現制冷,即當直流電通過N型和P型半導體組成的電偶對時,冷端吸收熱量,熱端釋放熱量。通過串聯數十至數百對電偶形成熱電堆,可實現-100℃至90℃的寬溫域控制,溫差電動勢率(塞貝克系數)和電阻率是決定制冷效率的關鍵參數。
(二)動態控制系統與梯度控溫
深冷機采用兩組PID控制回路(主、從回路)結合前饋PV技術,實現溫度梯度控制。例如,在芯片測試環節,設備可通過動態調整制冷功率,將測試環境溫度波動控制在±0.1℃以內,避免因溫度漂移導致測試數據失真。此外,全密閉循環管路設計配合呼吸孔,可延長導熱油壽命并防止油霧結霜,確保系統長期穩定運行。
二、應用場景:覆蓋封裝測試全流程
(一)封裝環節的溫度控制需求
塑封工藝(Molding)
環氧樹脂模塑過程中,模具溫度需嚴格控制。深冷機通過高精度控溫確保樹脂固化均勻性,避免因溫度波動導致元件翹曲或分層。
鍵合焊接(Die Bonding/Wire Bonding)
金線鍵合工藝中,鍵合頭溫度需在-10℃至+150℃間快速切換。深冷機通過液氮冷熱沖擊技術實現毫秒級響應,確保引線鍵合強度達標。
清洗與電鍍(Cleaning/Plating)
晶圓清洗環節需控制清洗液溫度以優化去污效果,電鍍工藝則需維持鍍液溫度穩定以確保鍍層均勻性。深冷機通過板式換熱器與管道式加熱器實現熱交換,將溫度波動控制在±0.5℃以內,使電鍍層厚度均勻性提升。
(二)測試環節的溫度保障需求
老化測試(Burn-in Test)
加速壽命試驗中,多工位測試臺需在-55℃至+175℃間循環。深冷機通過獨立溫控通道支持動態負載調節,使測試效率提升,同時降低因溫度應力導致的早期失效風險。
終檢(Final Inspection)
激光打標與電性能測試環節,深冷機為設備提供恒定環境溫度(±0.2℃),確保測試數據可重復性。例如,某功率器件測試項目通過深冷機實現-40℃至+125℃寬域控溫,產品直通率提高。
成品測試(Final Test, FT)
FT測試需模擬芯片實際工作場景,檢測功耗、溫度等參數。深冷機通過與測試機(Tester)和分選機(Handler)聯動,為待測芯片提供穩定環境,避免因溫度升高導致測試誤差。
三、核心價值:提升良率、效率與可靠性
(一)保障產品性能一致性
半導體器件對溫度敏感,微小波動可能導致電參數漂移。深冷機通過±0.1℃級精度控溫,消除熱應力對芯片的影響。
(二)提高生產效率與良率
縮短工藝周期
深冷機快速升降溫能力(如從室溫降至-40℃僅需5分鐘)可縮短封裝測試周期。
降低缺陷率
溫度波動是導致焊點空洞、樹脂分層等缺陷的主因之一。深冷機通過穩定控溫,使封裝缺陷率降低,顯著提升良品率。
(三)支持先進工藝與材料
寬禁帶半導體封裝
碳化硅(SiC)、氮化鎵(GaN)等材料對溫度更敏感,需在-50℃至+200℃間準確控溫。深冷機通過多級復疊制冷技術滿足此類需求,推動半導體器件的可靠封裝。
先進封裝技術兼容性
先進封裝工藝對溫度均勻性要求高。深冷機通過分布式溫控系統,確保晶圓級封裝(WLP)過程中溫度場一致性,支持2.5D/3D集成技術發展。
半導體深冷機通過高精度溫控、動態響應能力及多場景適配性,針對不同封裝測試場景,深冷機將提供從單通道(FLTZ變頻系列)到多通道(無壓縮機ETCU換熱單元)的模塊化解決方案,并支持非標定制,滿足AI芯片、汽車電子等新興領域的需求。
-
半導體
+關注
關注
335文章
28856瀏覽量
236789 -
封裝測試
+關注
關注
9文章
156瀏覽量
24276 -
冷水機
+關注
關注
0文章
90瀏覽量
7985
發布評論請先 登錄
半導體封裝設計與分析
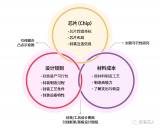
半導體制冷—— 2 1 世紀的綠色“冷源”
半導體的定義及其作用
射頻芯片測試的重要性及方法
半導體直冷機Chiller應用場景與選購指南
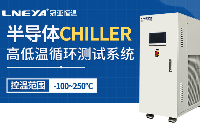
評論