在真無線立體聲(TWS)耳機爆發式增長的今天,直徑僅 6 毫米的微型揚聲器作為音頻轉換的核心部件,正經歷著 “體積微縮” 與 “性能升級” 的雙重挑戰。某專注于高端聲學元件的客戶,曾因手工焊接導致的品質波動,在 TWS 耳機供應鏈中舉步維艱。直到遇見大研智造激光錫球焊錫機,這場圍繞 “發絲級焊接” 的技術突圍戰,才迎來了破局的曙光。
一、微米級精度:6 毫米揚聲器的焊接極限挑戰
客戶生產的 TWS 無線耳塞驅動器 ——6 毫米微型揚聲器,堪稱聲學領域的 “納米級工程”:
物理極限:直徑 6mm、高度 3.8mm 的腔體內容納著音圈、振膜、磁路系統等 12 個精密部件,引線直徑僅 0.05mm,焊盤面積不足 0.2mm2,相當于在指甲蓋大小的空間內完成 8 組引線焊接;
性能指標:需滿足 110dB±3dB 的靈敏度、≤1% 的總諧波失真(THD),以及 - 40℃~85℃溫度循環下的穩定工作要求;
行業痛點:TWS 耳機市場年增長率超 30%,但手工焊接導致的 0.1mm 焊點偏差,會使揚聲器頻響曲線出現 ±5dB 波動,直接影響降噪耳機的主動降噪效果。
二、手工焊接:被放大的 “毫米級失誤”
在與大研智造合作前,客戶沿用了 3 年的手工焊接模式,逐漸暴露出三大致命短板:
(一)品質波動:看不見的 “聲學殺手”
焊工依賴 20 倍放大鏡進行操作,但連續作業 1 小時后,視覺疲勞導致的焊點偏移率高達 22%。2022 年季度質檢數據顯示:
虛焊引發的無聲故障占比 18%;
短路導致的雜音問題占比 15%;
過熱造成的振膜硬化使失真率超標案例占比 12%。這些問題導致客戶在某國際品牌驗廠時,首件合格率僅 65%,錯失百萬級訂單。
(二)效率瓶頸:產能爬坡的 “阿喀琉斯之踵”
手工焊接單只揚聲器需 4 分 15 秒,8 人班組日產能僅 800 只,無法滿足 TWS 耳機代工廠 4000 只 / 日的最低供貨要求。2023 年某電商大促期間,客戶因交付延遲賠付違約金達 120 萬元,更被列入 “風險供應商” 名單。
(三)成本黑洞:隱性損耗的 “蝴蝶效應”
人力成本:培養 1 名合格焊工需 3 個月,月薪達 1.2 萬元,且流失率高達 40%;
材料浪費:手工焊接的錫料利用率僅 75%,年損耗成本超 60 萬元;
品控成本:需投入 20% 的人力進行全檢,質檢成本占生產成本的 18%。
三、大研智造破局:從 “經驗焊接” 到 “數據焊接” 的進化
針對微型揚聲器的焊接痛點,大研智造技術團隊定制了 “微米級精密焊接解決方案”,通過三大核心技術重構焊接工藝:
(一)五維視覺定位系統:發絲級的 “空間定位”
硬件配置:集成 500 萬像素工業相機與激光三角測量模塊,構建 50μm 分辨率的坐標系,實現 ±0.01mm 的定位精度(相當于人類發絲直徑的 1/6);
算法突破:開發 “焊點特征增強算法”,即使在振膜反光、磁路陰影等復雜環境下,也能 0.3 秒內完成焊盤識別,解決了手工焊接 “憑手感對位” 的盲區;
應用實效:在 6mm 揚聲器的 0.2mm 焊盤焊接中,定位偏差率從手工焊接的 22% 降至 0.8%。
(二)脈沖激光動態調制技術:納秒級的 “能量手術刀”
能量控制:采用 915nm 半導體激光器,脈沖寬度可在 0.5-3ms 間動態調節,能量輸出穩定性達 ±2‰,精準控制焊點熔深在 50-80μm(約為 A4 紙厚度的 1/2);
熱管理創新:通過氣流動力學設計,將焊接熱影響區控制在 0.06mm2,低于音圈絕緣層的安全閾值,徹底解決了手工焊接導致的音圈電阻漂移問題(手工焊接漂移率 ±5%,大研方案控制在 ±0.3%);
工藝突破:針對揚聲器引線的鍍銀層特性,開發 “雙脈沖焊接” 模式:首脈沖 3ms 破除氧化層,次脈沖 1ms 完成冶金結合,焊點抗拉強度提升 40%,達 5N/mm2。
(三)智能錫球輸送系統:亞毫米級的 “物料精控”
送球精度:自主研發的真空渦流送球裝置,可穩定輸送 0.15-0.3mm 錫球,送球位置誤差≤±5μm,相當于在 6mm 揚聲器的焊盤上 “投放芝麻大小的錫球”;
防堵塞設計:采用納米涂層噴嘴與自動反吹清潔技術,噴嘴壽命達 50 萬次無堵塞,較傳統送球系統提升 3 倍;
物料適配:支持 SAC305、Sn96.5Ag3.0Cu0.5 等多種焊料,通過壓力傳感器實時監測送球壓力,確保不同批次錫球的焊接一致性。
四、打樣實測:從 “忐忑試產” 到 “驚艷交付”
2024 年,客戶帶著 “試試看” 的心態啟動打樣,卻收獲了遠超預期的效果:
(一)首件測試:顛覆認知的 “零缺陷”
外觀檢測:10 倍顯微鏡下,焊點呈完美的圓弧形,焊料浸潤角均在 35°-45°(IPC-A-610E 標準最優區間),無任何錫球飛濺或冷焊痕跡;
電性能測試:100% 通過 20Hz-20kHz 掃頻測試,諧波失真均值 0.8%,較手工焊接的 1.8% 提升顯著;
可靠性驗證:經過 85℃/85% RH 高溫高濕測試 500 小時,焊點電阻變化率≤1%,而手工焊接樣品的變化率達 8%。
(二)批量試產:效率與品質的 “雙重飛躍”
產能提升:單工位設備焊接速度達 1.5 秒 / 只,8 小時連續作業產能達 1920 只,是手工焊接的 3.2 倍;
良率突破:首周試產 10000 只,一次性良品率 99.2%,較手工焊接的 82% 提升 17.2 個百分點;
成本優化:錫料利用率提升至 98.5%,人力成本下降 60%,單只焊接成本從 1.2 元降至 0.45 元。
五、客戶價值:從 “合格供方” 到 “戰略伙伴”
打樣成功后,客戶經歷了從 “忐忑合作” 到 “深度綁定” 的轉變:
(一)市場突破:敲開高端供應鏈大門
某歐美頂級耳機品牌在驗廠時,被大研智造方案的 “焊點一致性” 征服,將客戶納入核心供應商體系,首年訂單量達 300 萬只;
客戶的揚聲器產品在國際音頻展上,憑借 “零焊接缺陷” 的優勢,獲得 “最佳聲學組件” 提名,品牌溢價提升 25%。
(二)長期價值:構建核心競爭力
客戶計劃采購 5 臺大研智造設備,組建全自動焊接產線,預計 2024 年產能突破 50 萬只 / 月,生產成本再降 30%;
通過大研智造的遠程運維系統,設備綜合效率(OEE)達 85%,較手工產線提升 40%,故障響應時間從 4 小時縮短至 15 分鐘。
六、行業啟示:微型化制造的 “破局密鑰”
6 毫米微型揚聲器的焊接案例,折射出精密制造領域的兩大趨勢:
(一)從 “事后檢測” 到 “實時控制”
集成的激光功率傳感器與紅外測溫模塊,構建了 “焊接參數 - 能量輸出 - 質量反饋” 的閉環控制,使焊接過程可控性提升 90%。
(二)從 “設備供應” 到 “工藝伙伴”
大研智造的價值不僅在于設備交付,更在于提供包含治具設計、工藝優化、系統集成的全流程解決方案,幫助客戶實現技術躍遷。
結語:當 “毫米級” 遇見 “微米級”
6 毫米微型揚聲器的焊接升級,是一場 “毫米級器件” 與 “微米級工藝” 的完美邂逅。大研智造激光錫球焊錫機,不僅解決了客戶的品質痛點,更以技術創新重新定義了微型揚聲器的制造標準。在 TWS 耳機滲透率突破 40% 的今天,這樣的精密焊接解決方案,正成為聲學元件制造商搶占市場的 “核心武器”。
審核編輯 黃宇
-
激光
+關注
關注
20文章
3456瀏覽量
66095 -
焊接
+關注
關注
38文章
3412瀏覽量
61255
發布評論請先 登錄
激光錫焊用多少瓦的激光器?大研智造全面解析功率選擇策略 —— 從 5W 到 600W,精準匹配不同場景的焊接需
大研智造激光錫球焊標準機:精密焊接技術的行業標桿——解密單工位激光錫球焊機的創新優勢與應用價值
從“制造”到“智造”:大研智造激光錫球焊錫機如何定義焊接新范式?
解析大研智造激光錫球焊錫機助力醫療設備精密焊接的獨特優勢
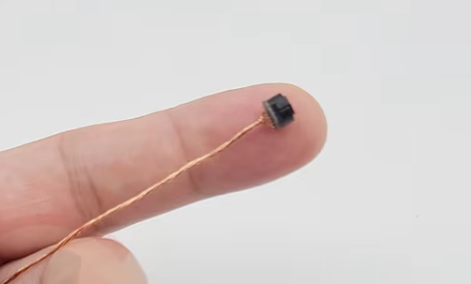
評論