在智能制造與智慧物流領域,AGV(Automated Guided Vehicle)無人叉車已成為提升倉儲效率的核心裝備。其價值不僅在于自主搬運能力,更體現在與各類倉儲設備、系統的無縫對接能力上。本文將詳細解析 AGV 無人叉車的五大典型對接方式,揭示其如何通過技術集成實現物流全流程自動化。
一、與輸送線對接:構建動態物流閉環
技術實現:
AGV 通過激光雷達或視覺傳感器識別輸送線位置,配合高精度定位技術(如二維碼導航、SLAM 激光導航)實現±10mm級對接精度。當輸送線傳輸物料至指定節點時,AGV 自動行駛至接駁口,通過頂升機構完成物料承接或釋放。
應用場景:
①生產車間線邊倉:AGV與滾筒輸送線對接,實時抓取生產線完工的變速箱總成,直接轉運至裝配線,減少人工轉運造成的15%效率損耗。
②智能分揀中心:與交叉帶式分揀機對接,AGV自動將整托盤物料拆解為小件包裹,分揀效率提升至傳統人工的4倍。
核心優勢:
①連續作業能力:24小時無間斷接駁,消除人工接駁導致的節拍中斷;
②柔性適配:支持多種輸送線速度(0.5-2m/s),通過軟件參數調整即可兼容不同產線。
二、與貨架系統對接:精準存取的底層邏輯
技術實現:
①傳統貨架(平面庫):
AGV通過貨叉側移、前傾/后傾功能,精準插入貨架底部托盤孔(誤差≤5mm),配合提升機構完成貨物存取。部分車型配備機械臂式貨叉,可適應不同深度貨架。
②智能立體庫(AS/RS):
與堆垛機、穿梭車聯動,AGV 負責庫前接駁,將物料送入立體庫巷道口。例如某電氣制造企業,通過AiTEN AGV與立體倉庫的聯動,成功實現了物料轉運與成品入庫的自動化,顯著提升生產效率。
海豚之星案例:
AGV與立體倉庫穿梭車聯動實現物料自動轉運案例
三、與電梯/升降機對接:跨樓層物流的無縫銜接
技術實現:
AGV 通過無線通信協議與電梯控制系統深度集成,實現“自主呼梯-精準平層-安全進出”全流程自動化。典型流程包括:
AGV 接近電梯時,通過RFID標簽或視覺識別電梯編號,發送呼叫指令;
電梯到達后,AGV通過激光雷達掃描電梯地板平整度,確保平層誤差<3mm;
進出電梯過程中,AGV 實時監測轎廂內障礙物,遇突發情況 0.2 秒內急停。
海豚之星機器人應用案例:
某新能源行業公司,需要跨樓層搬運,費時費力,采用海豚之星APe15搬運機器人進行搬運并放貨至電梯,提高了倉庫搬運效率和智能化水平,降低人力成本,確保貨物準確搬運。
四、與協作機器人對接:柔性生產的黃金搭檔
技術實現:
AGV與機械臂、碼垛機器人通過統一調度系統(如RDS機器人調度系統)協同作業:
①上下料場景:AGV將滿料托盤送至協作機器人工作站,機械臂自動拆垛并裝配零件,AGV同步取走空托盤;
②混線生產:在小家電工廠,AGV根據生產工單,向不同產線配送定制化物料組合,配合機器人實現“多品種、小批量”柔性生產,換線時間從2小時壓縮至15分鐘。
協同優勢:
①人機分工優化:AGV負責重體力搬運,機器人專注精密操作,人員轉向工藝監控;
②數據互通:通過MES系統實時同步生產進度,AGV動態調整搬運優先級,避免物料積壓。
五、與WMS系統對接:數字化物流的神經中樞
技術實現:
①任務下發:WMS根據庫存數據自動生成搬運指令(如 “將A區3號貨架托盤移至B區5號揀貨位”),通過AGV調度系統分配至最近AGV;
②狀態反饋:AGV實時回傳位置、任務進度、電池電量等數據,WMS 動態更新庫存狀態,避免人工錄入導致的數據誤差;
③數據分析:通過歷史搬運數據訓練算法,優化AGV路徑規劃,減少30%無效行駛里程。
海豚之星應用案例:
海豚之星基于某汽車零部件制造企業的現場環境和生產需求,定制高效智能搬運解決方案,采用輕小型搬運機器人MP10s作為核心設備,并配合海豚之星的WCS設備對接系統、RDS調度系統和LMS庫位管理系統,實現全流程自動化,作業效率提高50%以上,生產流程更加流暢。
汽車工廠物流管理混亂?海豚之星定制方案實現倉儲利用率提升30%,管理效率升35%
六、結語
從單一搬運工具到智能物流樞紐,AGV無人叉車的進化史本質是對接能力的升級史。通過與物理設備、數字系統的深度融合,AGV正在重塑“人-機-物”的協作關系,讓倉儲物流從“勞動密集型”向“技術驅動型”躍遷。未來,隨著5G、AI大模型的應用,AGV將實現更復雜場景的自主決策與動態協同,成為智能制造的核心基礎設施。
原文:海豚之星機器人官網
審核編輯 黃宇
-
AGV
+關注
關注
27文章
1436瀏覽量
42231
發布評論請先 登錄
聯核CBD20H快運版搬運型無人AGV叉車產品介紹/參數/優勢/應用場景
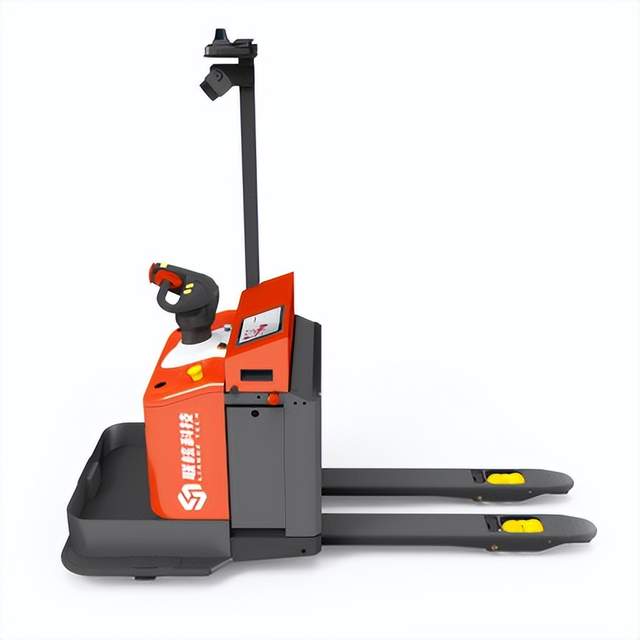
評論