汽車零部件開發項目管理是一個涉及多環節、多部門協作的復雜過程,需從項目啟動到交付全流程進行科學規劃與管控。以下從核心流程、關鍵要素、管理工具及挑戰與應對策略四方面展開說明:
一、核心流程:汽車零部件開發項目全周期管理
1. 項目啟動與規劃階段
明確需求與目標
與主機廠(OEM)或客戶溝通,確定零部件技術規格(如尺寸、性能、材料)、質量標準(如 IATF 16949)、交付周期及成本預算。示例:開發新能源汽車電機控制器時,需明確電壓平臺、功率輸出、能效要求等。
組建跨職能團隊
成員包括項目經理、設計工程師、工藝工程師、質量工程師、采購人員、供應鏈專員等。
制定項目計劃
用甘特圖劃分關鍵節點:設計凍結(DFM)、樣件制作(Prototype)、臺架測試(Bench Test)、整車匹配驗證(Vehicle Integration)、量產爬坡(SOP Ramp-up)等。示例:某底盤零部件項目計劃周期為 18 個月,其中設計階段占 6 個月,驗證階段占 8 個月,量產準備占 4 個月。
2. 設計與開發階段
方案設計與評審
運用 CAD/CAE 工具(如 CATIA、ANSYS)完成三維建模與仿真分析(如強度、振動、熱管理),通過 DFMEA(設計失效模式分析)識別潛在風險。召開設計評審會(DR1/DR2/DR3),邀請客戶、供應商及內部團隊確認方案可行性。
樣件制作與驗證
采用 3D 打印、快速模具等技術制作樣件,進行功能測試(如零部件耐久性試驗)和法規認證(如 ISO 26262 功能安全認證)。示例:電子零部件需通過 EMC(電磁兼容)測試,確保不干擾整車其他系統。
設計變更管理(ECN)
若客戶需求調整或測試中發現問題,需通過標準化流程評估變更影響(如成本、交期、質量),經審批后更新圖紙與 BOM 表。
3. 量產準備與交付階段
工藝開發與產能建設
設計生產流程(如沖壓、焊接、注塑工藝),制定 PFMEA(過程失效模式分析),優化設備布局與工裝夾具。建立生產線并進行試生產(PPAP 階段),驗證產能(如單班產量、設備稼動率)與良率(目標≥99%)。
供應鏈管理
選定二級供應商(如原材料、標準件供應商),簽訂質量協議(如 PPAP、GP-12 早期遏制計劃),確保零部件準時交付。應對突發風險(如芯片短缺):建立安全庫存、開發備選供應商、調整生產計劃。
量產與持續改進
啟動 SOP(量產啟動),監控初期生產質量(如采用 SPC 統計過程控制),收集售后反饋(如市場抱怨、保修數據),推動 DVP(設計驗證計劃)迭代優化。
二、關鍵要素:
項目成功的核心驅動力
1. 質量管理體系遵循 IATF 16949 標準,建立 APQP(產品質量先期策劃)流程,確保開發各階段符合客戶要求。
重點管控:
PPAP(生產件批準程序):提交全尺寸檢測報告、材料成分分析、性能測試數據供客戶批準。
8D 報告:針對重大質量問題(如量產初期批量缺陷),通過團隊協作制定糾正措施。
2. 成本與進度控制
成本管理
運用 VA/VE(價值分析 / 價值工程)優化設計,降低材料與工藝成本(如采用輕量化材料替代傳統鋼材)。監控項目預算,避免超支(如設計變更導致模具返工成本增加)。
進度管理
用關鍵路徑法(CPM)識別影響交付的瓶頸環節(如長周期設備采購),通過趕工或資源協調確保節點按時完成。每周召開項目例會,更新狀態報告(如燃盡圖、掙值管理 EVM),及時預警延期風險。
3. 跨部門協作與溝通
溝通機制
建立標準化溝通渠道:每日站會(Scrum 模式)、每周進度報告、每月高層匯報。使用項目管理工具(如 Jira、Microsoft Project)共享信息,避免信息孤島。
客戶與供應商協同
定期與客戶對齊需求(如設計評審、階段驗收),與供應商同步開發進度(如聯合解決技術難題)。
三、管理工具與技術
1. 數字化工具
PLM(產品生命周期管理系統):管理圖紙、BOM、變更記錄,實現開發流程可視化(如達索 Enovia)。
MES(制造執行系統):量產階段監控設備狀態、工藝參數、質量數據,實時反饋生產異常。
AI 與大數據應用:通過機器學習預測零部件疲勞壽命,或利用大數據分析供應鏈風險(如物流延遲概率)。
2. 敏捷開發方法
對電子類零部件(如車載軟件)采用敏捷開發,將大任務拆解為短周期迭代(如 2 周一個 Sprint),快速響應需求變更。示例:OTA 升級功能開發中,通過敏捷測試縮短驗證周期,提前 2 個月完成交付。
四、挑戰與應對策略
1. 挑戰類型
技術復雜度高:新能源零部件(如電驅動系統、電池組件)涉及多學科融合,開發難度大。
法規與環保要求嚴格:需滿足歐盟 REACH、中國雙積分政策等,增加合規成本。
供應鏈波動:全球芯片短缺、原材料價格上漲(如鋰、鈷)導致交付風險。
客戶需求變更頻繁:主機廠車型迭代加速,可能在開發后期調整設計要求。
2. 應對策略
技術創新:與高校、科研機構合作開發前沿技術(如固態電池、SiC 芯片),建立技術預研機制。
合規管理:提前識別法規要求,在開發初期納入設計(如輕量化滿足油耗標準)。
供應鏈韌性建設:實施多元化采購策略,與核心供應商建立戰略合作伙伴關系(如簽訂長期產能保障協議)。
需求變更管理:在合同中明確變更范圍與成本分攤機制,采用模塊化設計降低變更影響。
總結
汽車零部件開發項目管理需以質量為核心,以進度與成本為約束條件,通過跨部門高效協作、數字化工具應用及風險預控,確保項目按時、按質、低成本交付。未來,隨著智能化、電動化趨勢深化,項目管理將更強調敏捷性、生態協同(如與軟件供應商、充電設施企業合作)及可持續性(綠色材料、低碳工藝應用)。
審核編輯 黃宇
-
汽車零部件
+關注
關注
0文章
337瀏覽量
17642
發布評論請先 登錄
如何給汽車零部件進行疲勞耐久測試?
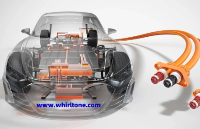
尋跡智行亮相2025汽車零部件物流大會,共探智慧物流新思路
汽車零部件需要做哪些試驗?

智能零部件管理助力中電思儀的標準化管理
至純科技珠海半導體零部件清洗項目啟動
從汽車零部件檢測看變焦、變倍鏡頭應用差異
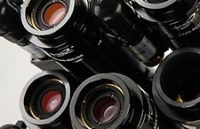
AIM有限公司有效控制零部件的野蠻增長并優化企業流程
遠程 IO 模塊:汽車零部件產線的高效生產引擎
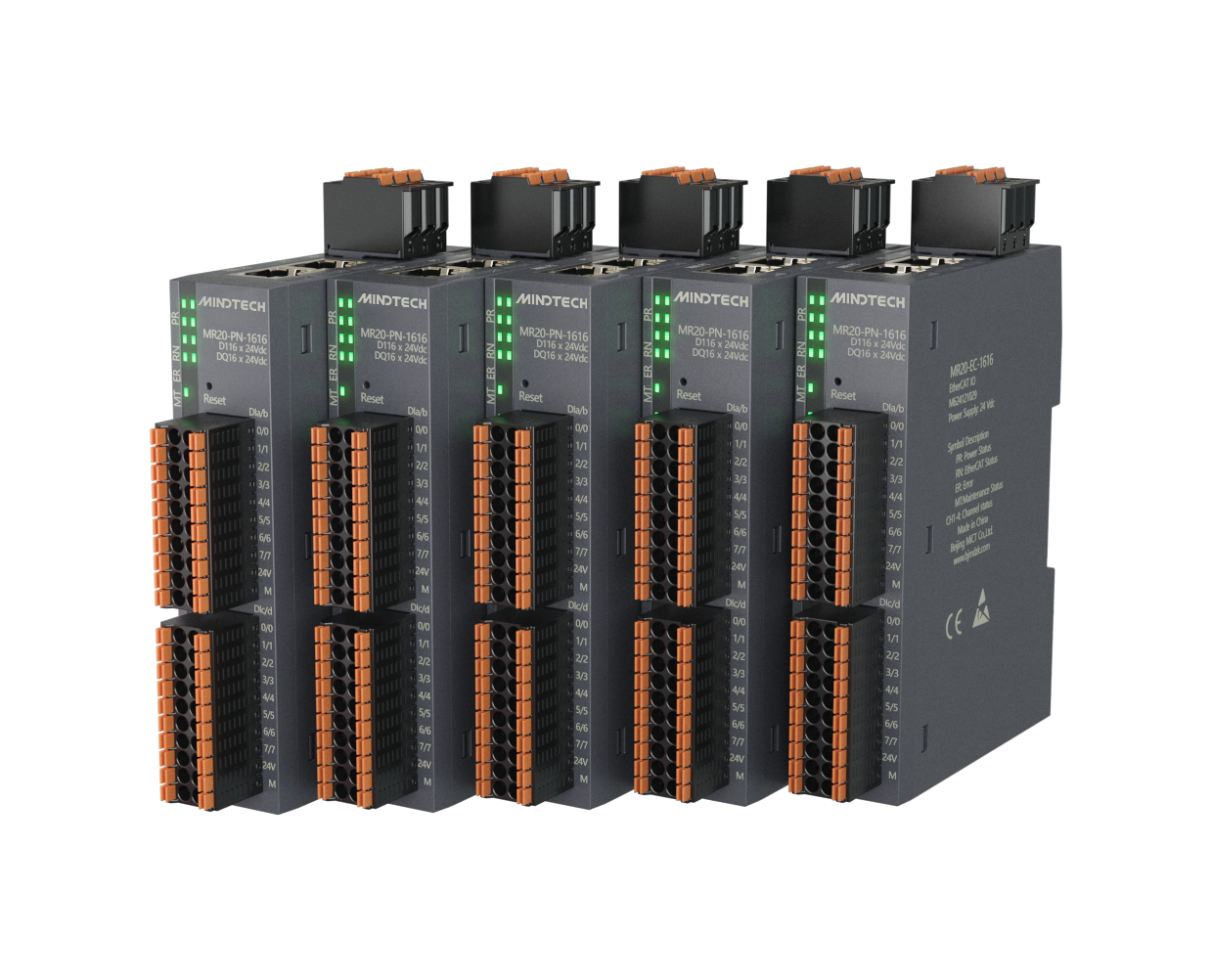
評論