??第一篇:為什么90%工廠做不好注塑機數據采集?傳統點表的三大致命傷??
在制造業數字化轉型的浪潮中,“設備數據采集”被公認為智能工廠的“地基”——只有先讓設備“開口說話”,才能分析優化工藝、降低能耗、預測故障。但對于注塑機這一工業母機的核心裝備,??90%的工廠卻卡在了第一步:數據采集難如登天??。
某浙江汽車零部件廠的負責人張總曾向筆者吐槽:“去年花20萬找服務商做注塑機能耗監控,結果3個月才上線3臺設備!剩下的47臺全是‘啞巴機’,要么協議對不上,要么點表配錯了,最后只能不了了之。”這樣的案例絕非個例——傳統數據采集的“點表依賴癥”,正成為中小企業數字化轉型的最大攔路虎。
??痛點一:“沒有點表,寸步難行”——技術門檻卡死90%中小企業??
所謂“點表”,是工業設備數據采集的“翻譯字典”:每臺設備的傳感器、按鈕、儀表都有對應的“地址碼”(如Modbus協議的4xxxx寄存器),工程師需提前整理出這份“地址-參數”對照表(即點表),才能讓網關正確讀取數據。
但對中小企業來說,??“搞定點表”比“買設備”還難??:
??懂協議的人才稀缺??:注塑機常用協議包括Modbus RTU/TCP、西門子S7-200/300/400、Profinet、歐姆龍FINS等,這些協議文檔動輒上百頁,參數配置復雜(如寄存器類型、數據格式、校驗方式)。中小企業普遍沒有專職工業通訊工程師,找外部服務商又面臨“技術壟斷”——某服務商曾報價“單臺設備點表配置費5000元”,50臺就是25萬。
??點表易出錯,返工成本高??:即使勉強配出點表,現場調試時也常因設備型號差異(如同品牌不同系列)、固件版本更新(如升級后寄存器地址變更)導致數據錯位。某3C電子廠曾因點表配置錯誤,誤將“模具溫度”讀成“液壓油溫度”,導致批量產品飛邊,損失超10萬元。
??深控技術不需要點表工業網關如何破局??? 深控技術的核心突破是“??自動協議解析+自適應適配??”:通過內置的“設備特征庫”(覆蓋90%主流注塑機通信報文規律),網關無需人工配置點表,插入設備接口后,能在5分鐘內自動識別設備類型(如海天、伊之密)、匹配通信協議,并生成標準化數據接口(如JSON、MQTT)。即使是完全陌生的設備(如某小廠定制機型),網關也能通過“報文特征學習”功能,在1小時內完成適配——真正實現“即插即用”。
??痛點二:“品牌壁壘,協議打架”——設備混雜讓采集成了“拼圖游戲”??
中國注塑機市場品牌高度分散,既有海天、伊之密、震雄等國產龍頭(合計市占率超60%),也有住友、日鋼、發那科等日系/歐系高端品牌(主打精密注塑),還有大量中小廠定制機型。不同品牌的注塑機,??通信協議、接口類型、數據格式差異極大??,導致數據采集成了“跨語言翻譯”難題。
以最常見的“協議不兼容”為例:
某東莞家電注塑件廠曾同時使用海天、伊之密、震雄三種品牌設備,服務商坦言:“海天的Modbus表配了2周,伊之密的Profinet連不上,震雄的脈沖信號根本不敢碰——光調試就花了45天,客戶都快取消了。”
??深控技術不需要點表工業網關如何破局??? 深控網關內置??多協議自適應引擎??,支持Modbus RTU/TCP、西門子S7(全系列)、Profinet、CC-Link、EtherCAT等30+種主流工業協議,覆蓋90%以上注塑機品牌(詳見下表)。即使是混合產線(如同時有海天MA800、伊之密C3、震雄J120),網關也能自動識別每臺設備的協議類型,無需為不同品牌單獨調試——真正實現“一臺網關管所有”。
??痛點三:“耗時耗力,成本爆炸”——傳統采集的隱性代價遠超想象??
傳統點表采集的“時間成本”和“隱性損耗”,往往被企業低估:
??實施周期長??:單臺設備點表配置+調試平均需2-3天(含停機等待),50臺設備就是100-150個工作日。某中型制造企業曾因采集項目延誤,導致MES系統上線推遲2個月,直接損失訂單300萬元。
??停機風險高??:傳統采集需接入設備控制電路(如PLC輸入輸出點),部分老舊設備(如10年以上的震雄機型)線路老化,調試時稍有不慎就會觸發故障停機。某玩具廠曾因接線錯誤導致注塑機螺桿斷裂,維修費用高達8萬元。
??后期維護難??:設備更換或升級(如更換PLC模塊)后,點表需重新配置;新增設備(如新增10臺高速機)時,又需重復“調研-配置-調試”流程。某汽車飾板廠每年因設備迭代,需額外支付服務商15萬元維護費。
??深控技術不需要點表工業網關如何破局??? 深控技術網關采用??物理層信號直采技術??,無需接入設備控制電路(僅通過設備自帶的RS485、以太網等標準接口連接),避免了接線風險;同時支持“零停機部署”——可在設備生產間隙(如換模、待料時)快速安裝,單臺設備接入僅需30分鐘。更關鍵的是,網關支持“自動發現新設備”功能,產線新增設備時,系統會自動識別并納入采集體系,??后期維護成本降低80%??。
??案例實證:傳統點表的“坑”,深控如何一一填平???
為驗證深控技術不需要點表工業網關的價值,我們在3家典型工廠進行了實地測試:
??案例1:廣東某汽車零部件廠(混用海天、伊之密)??
??售前調研痛點??:50臺注塑機(海天MA800、伊之密C3各25臺),服務商報價“45天完成,總費用28萬”(含點表配置+調試)。
??深控技術方案??:部署無點表網關,無需人工配置點表;現場測試:接入海天MA800(Modbus TCP)耗時25分鐘,接入伊之密C3(西門子S7)耗時30分鐘,全程無停機。
??效果??:部署周期縮短至5天,總費用僅8萬元;首月能耗成本下降8%(通過實時監控發現12臺設備“待機能耗異常”)。
??案例2:浙江某3C電子代工廠(進口日系注塑機)??
??售前調研痛點??:20臺日本住友SE-120機型(CC-Link協議+數據加密),服務商以“協議未公開”為由拒絕接單。
??深控技術方案??:網關通過“報文特征學習”功能,自動解析住友SE系列的私有協議;部署時避開生產高峰,2天內完成20臺設備接入。
??效果??:數據完整率99.5%,工藝員通過手機APP實時監控模具溫度,產品飛邊率下降4%;后續新增5臺同品牌設備,僅需1小時完成適配。
??案例3:江蘇某鄉鎮注塑件廠(老舊震雄機型)??
??售前調研痛點??:8臺10年震雄J80機型(無PLC、僅脈沖信號輸出),電工不懂工業協議,擔心“接錯線燒機器”。
??深控技術方案??:網關采用“物理層信號直采”技術,通過設備自帶的模擬量接口(4-20mA電流信號)直接采集壓力數據;電工按說明書半小時完成安裝。
??效果??:關鍵參數(射膠壓力)偏差率從±5%降至±1%,客戶投訴減少40%;老板主動為新增的5臺設備全部標配深控網關。
??結語:數據采集的“零門檻”,才是制造業數字化的起點??
傳統點表的“致命傷”,本質是工業物聯網早期的“技術壁壘”——依賴人工經驗、受限于設備差異、成本高企。而深控技術的“不需要點表工業網關”,通過“自動協議解析+多協議兼容+物理層直采”,徹底打破了這些壁壘。
對中小企業來說,這意味著:??不用再等3個月部署,不用再花20萬找服務商,不用再擔心設備不兼容??——只需要一臺網關,就能讓沉默的注塑機“開口說話”,讓數字化轉型的第一步,變得簡單、快速、可控。
?審核編輯 黃宇
-
數據采集
+關注
關注
40文章
7117瀏覽量
116242
發布評論請先 登錄
注塑機數據采集有哪些痛點難點?如何解決?
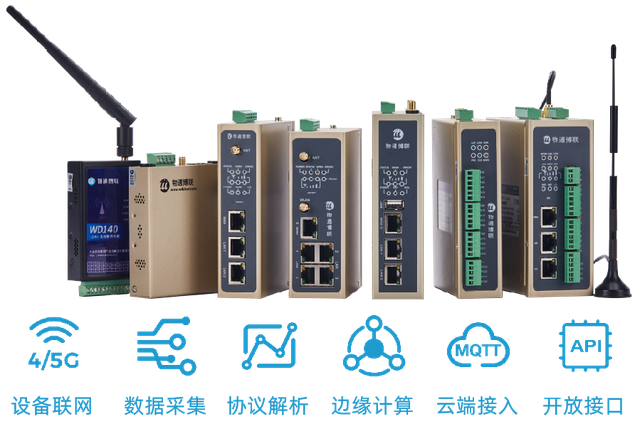
科強注塑機如何數據采集到MES系統上
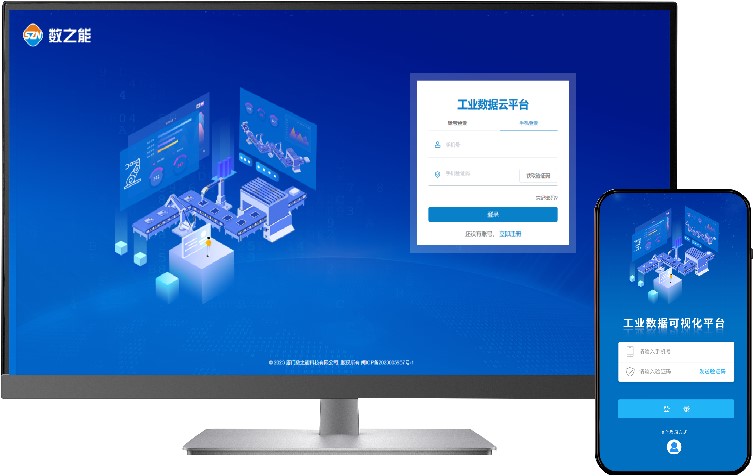
注塑機數據采集網關支持接入哪些品牌
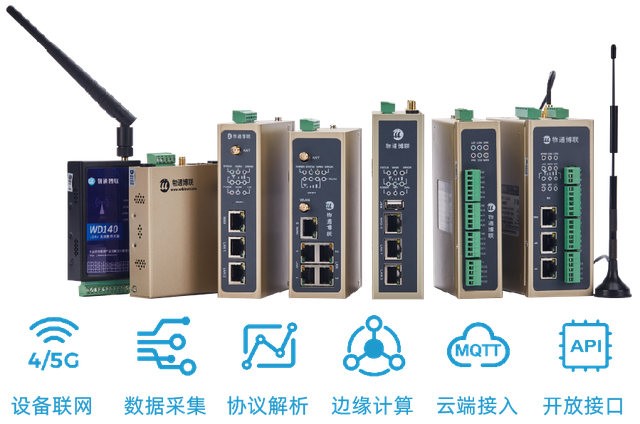
注塑機數據采集有哪些方式?如何實現?
注塑機數據采集網關可以采集什么數據?實現什么功能?
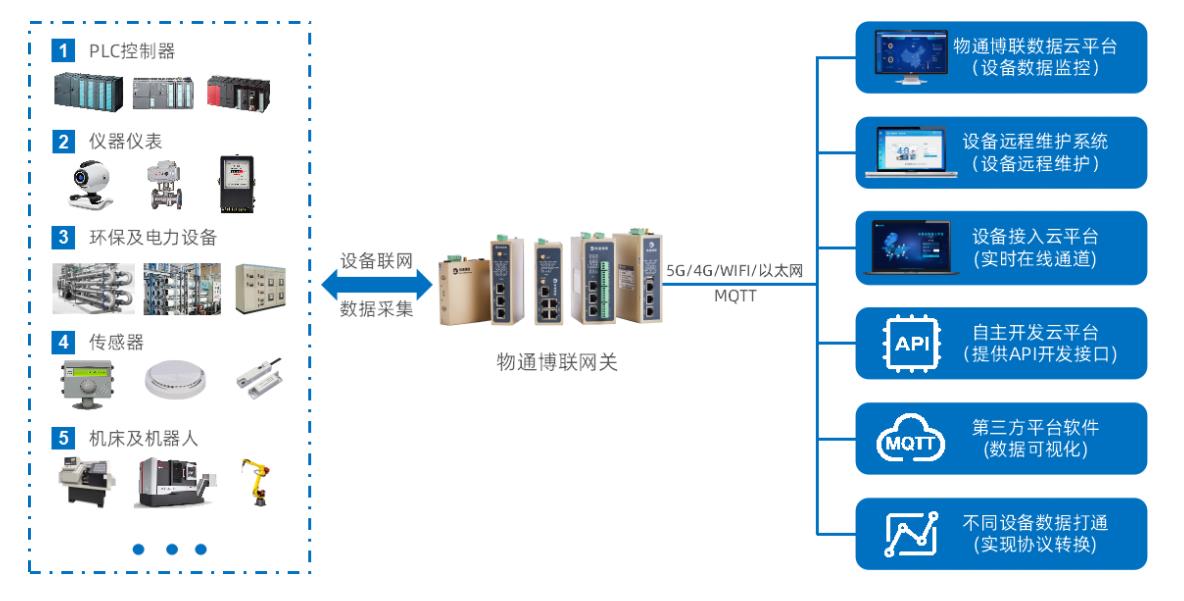
注塑機數據采集物聯網網關可以實現什么功能
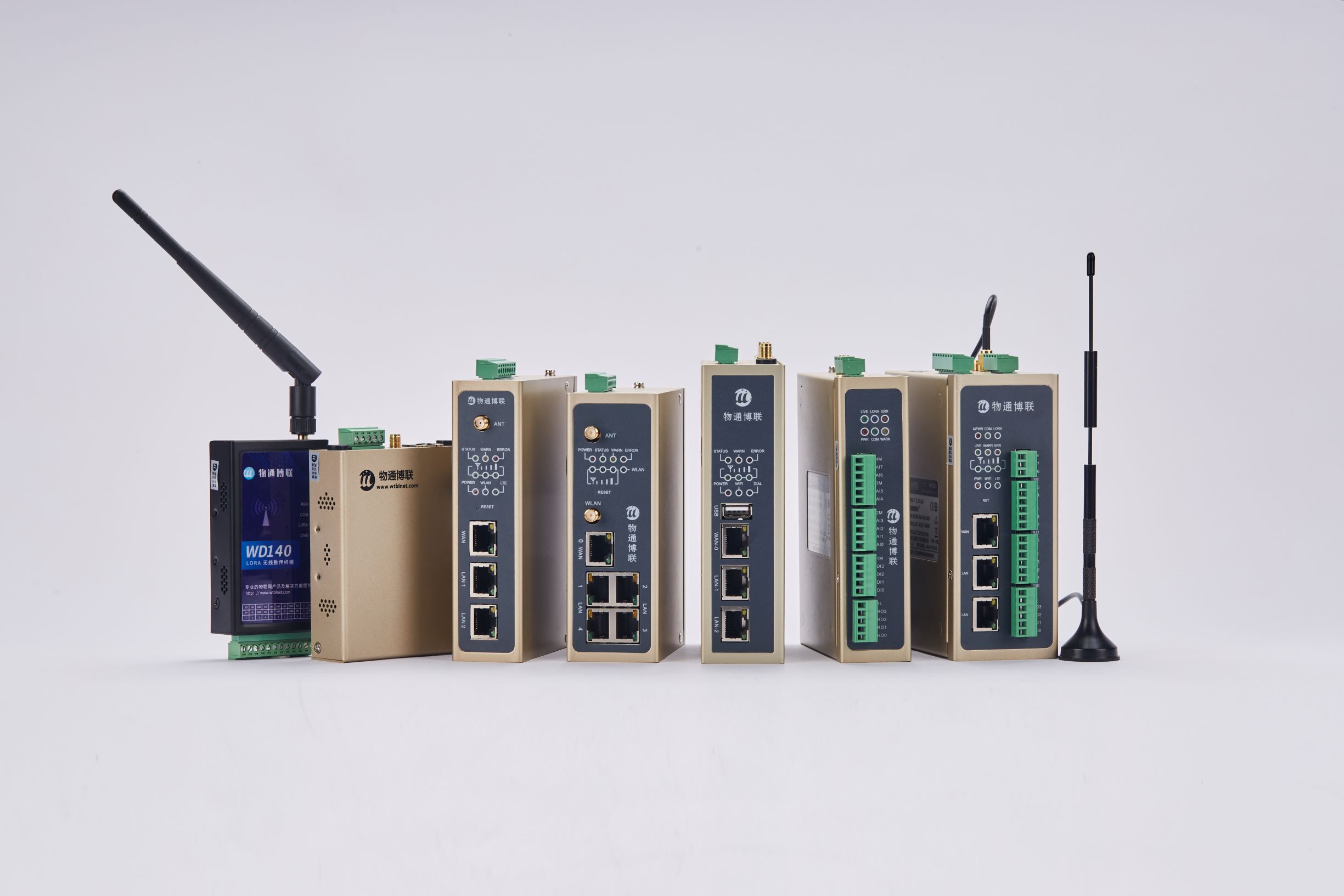
注塑機數據采集物聯網解決方案
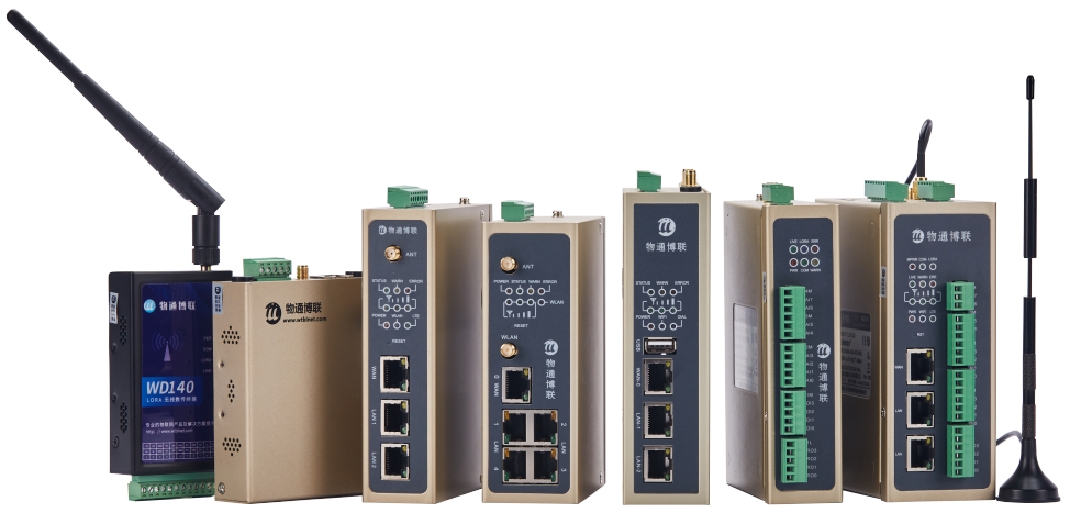
評論