一、引言
碳化硅(SiC)作為第三代半導體材料的代表,以其卓越的物理化學性能,在新能源汽車、軌道交通、5G 通信等關鍵領域展現出不可替代的作用。然而,SiC 材料硬度高、脆性大的特性,給其襯底切割加工帶來了極大挑戰。傳統切割方法存在切割精度低、效率慢、厚度均勻性差等問題,嚴重制約了 SiC 器件的性能與生產規模。在此背景下,開發基于機器視覺的碳化硅襯底切割自動對刀系統,并實現厚度均勻性控制,對推動 SiC 產業發展具有重要意義。
二、系統總體設計
自動對刀系統主要由機器視覺模塊、運動控制模塊、切割執行模塊和控制系統組成。機器視覺模塊采用高分辨率工業相機與定制光學鏡頭,實時采集切割區域圖像。運動控制模塊通過精密電機與絲杠導軌,精準控制切割刀具的位置與進給速度。切割執行模塊根據不同切割工藝(如金剛線切割、激光切割等)選擇相應刀具。控制系統整合各模塊信息,實現自動化運行。
三、機器視覺對刀原理與實現
3.1 圖像采集與預處理
工業相機以固定幀率采集切割區域圖像,圖像經灰度化、濾波、增強等預處理操作,提升圖像質量,凸顯襯底與刀具邊緣特征,為后續特征提取做準備。例如,采用高斯濾波去除圖像噪聲,直方圖均衡化增強圖像對比度。
3.2 特征提取與匹配
利用邊緣檢測算法(如 Canny 算法)提取襯底邊緣輪廓與刀具特征點。通過模板匹配技術,將實時采集圖像中的刀具特征與預先存儲的標準刀具模板進行匹配,確定刀具實際位置與姿態。當檢測到刀具位置偏差時,控制系統計算補償量并發送指令給運動控制模塊,實現刀具自動調整。
四、厚度均勻性控制策略
4.1 進給量動態調節
碳化硅襯底切割過程中,依據切割深度、刀具磨損狀態等因素動態調整進給量。切割起始階段,材料表面完整,刀具與材料接觸狀態穩定,可采用較大進給量提高加工效率。隨著切割深入,刀具磨損加劇,材料內部應力分布改變,此時逐步減小進給量,能有效控制切割力在合理范圍,維持材料均勻去除,保證厚度均勻性。構建以切割深度為自變量,進給量為因變量的梯度調節函數,通過傳感器實時監測切割深度、刀具振動、切割力等參數,將數據反饋至控制系統,由控制系統依據預設的梯度調節模型,動態調整進給量。
4.2 切割參數優化
通過實驗與仿真相結合的方式,建立切割參數(如切割速度、進給量、切割功率等)與厚度均勻性的映射關系模型。利用該模型,針對不同規格的碳化硅襯底,優化切割參數組合,使切割過程中材料去除均勻,降低厚度偏差。例如,對于較薄的襯底,適當減小切割速度與進給量;對于硬度更高的碳化硅材料,調整切割功率與冷卻條件,確保切割過程穩定,提升厚度均勻性。
高通量晶圓測厚系統運用第三代掃頻OCT技術,精準攻克晶圓/晶片厚度TTV重復精度不穩定難題,重復精度達3nm以下。針對行業厚度測量結果不一致的痛點,經不同時段測量驗證,保障再現精度可靠。?
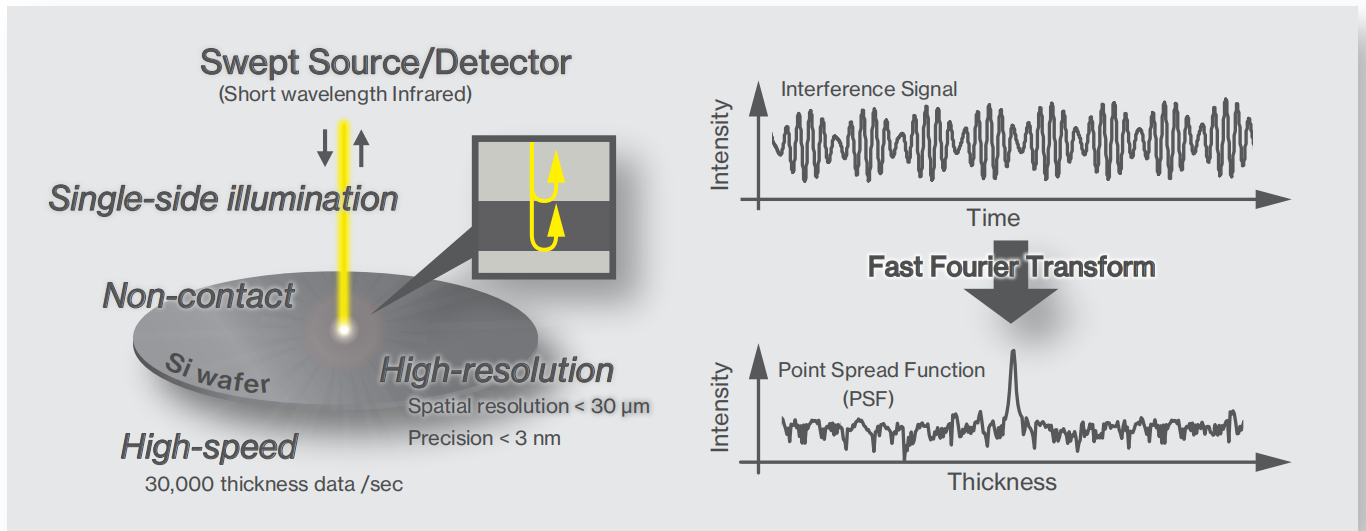
我們的數據和WAFERSIGHT2的數據測量對比,進一步驗證了真值的再現性:
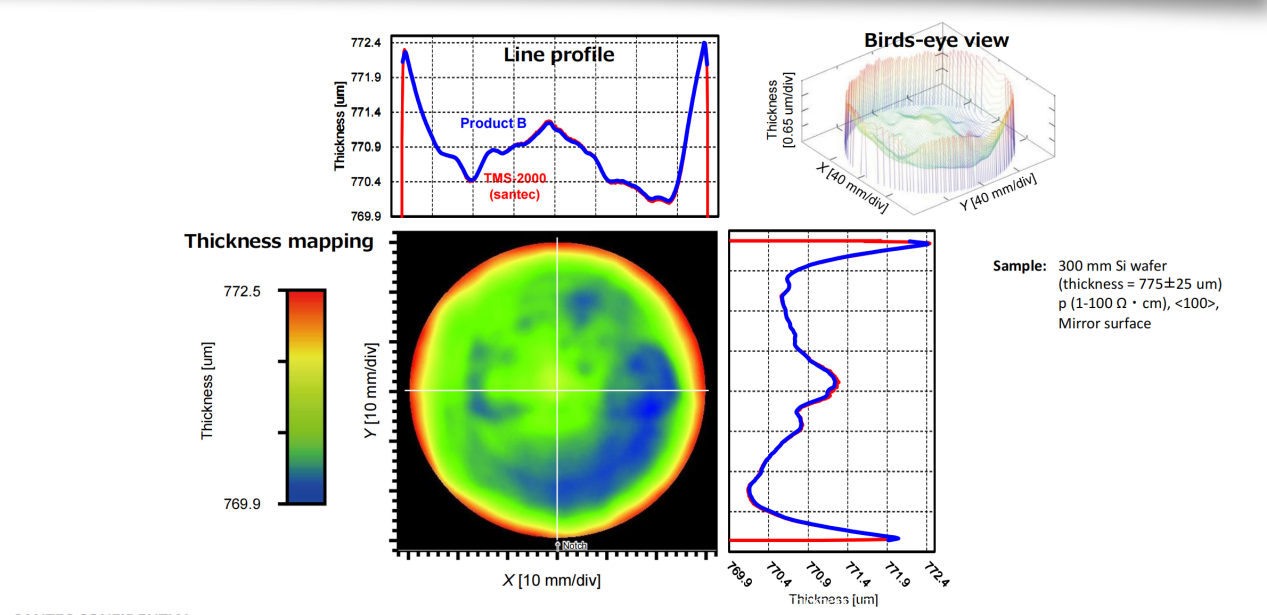
(以上為新啟航實測樣品數據結果)
該系統基于第三代可調諧掃頻激光技術,相較傳統雙探頭對射掃描,可一次完成所有平面度及厚度參數測量。其創新掃描原理極大提升材料兼容性,從輕摻到重摻P型硅,到碳化硅、藍寶石、玻璃等多種晶圓材料均適用:?
對重摻型硅,可精準探測強吸收晶圓前后表面;?
點掃描第三代掃頻激光技術,有效抵御光譜串擾,勝任粗糙晶圓表面測量;?
通過偏振效應補償,增強低反射碳化硅、鈮酸鋰晶圓測量信噪比;
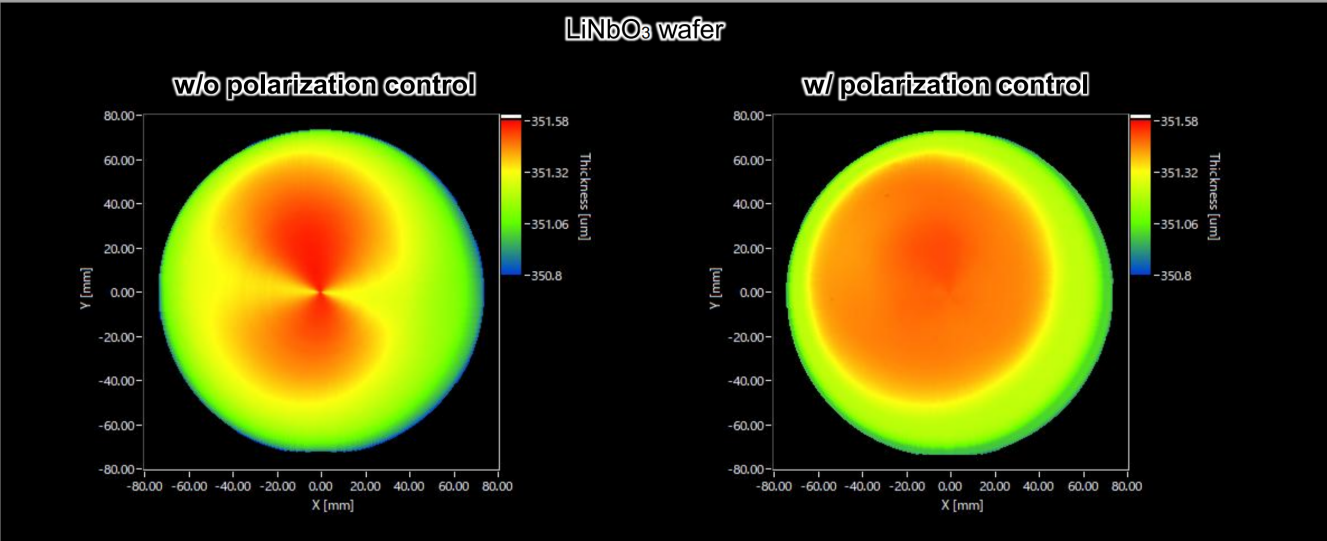
(以上為新啟航實測樣品數據結果)
支持絕緣體上硅和MEMS多層結構測量,覆蓋μm級到數百μm級厚度范圍,還可測量薄至4μm、精度達1nm的薄膜。
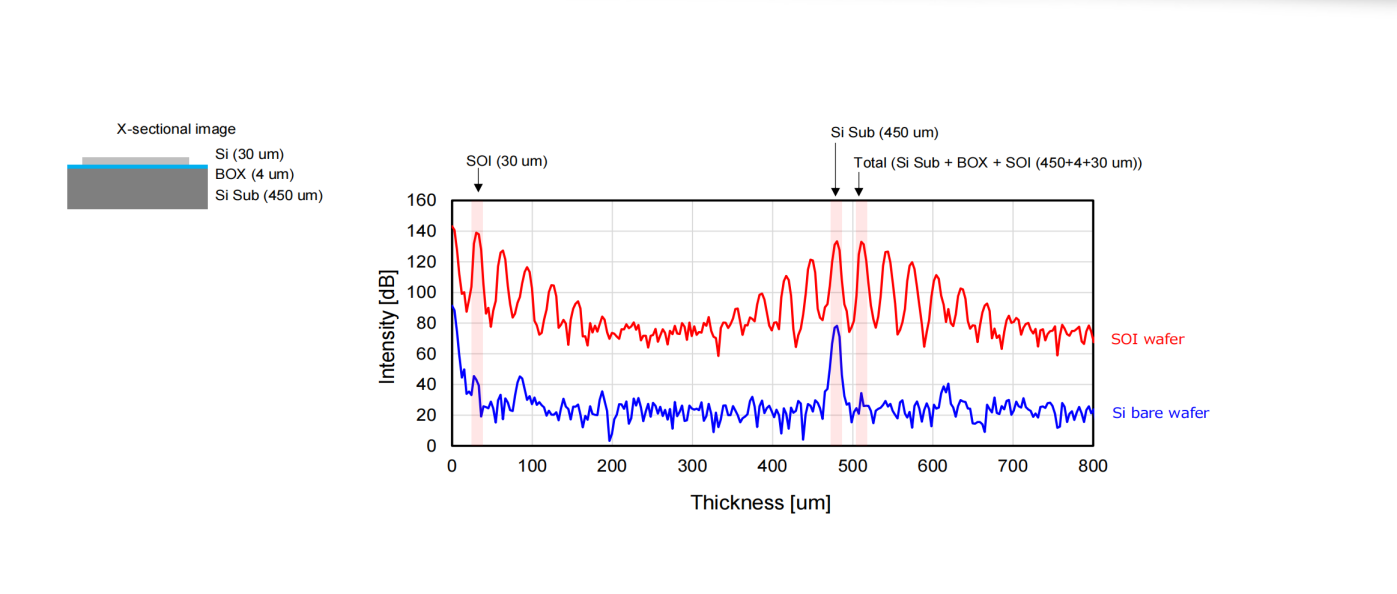
(以上為新啟航實測樣品數據結果)
此外,可調諧掃頻激光具備出色的“溫漂”處理能力,在極端環境中抗干擾性強,顯著提升重復測量穩定性。
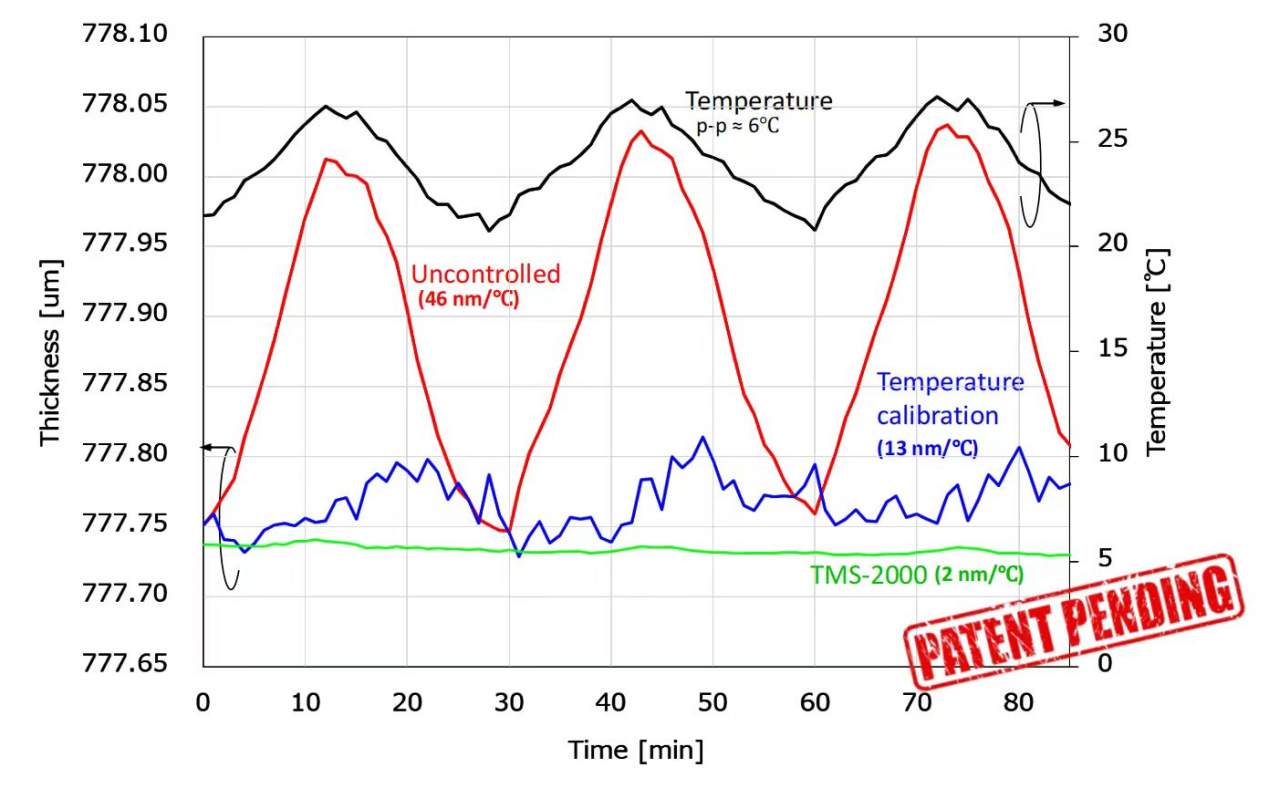
(以上為新啟航實測樣品數據結果)
系統采用第三代高速掃頻可調諧激光器,擺脫傳統SLD光源對“主動式減震平臺”的依賴,憑借卓越抗干擾性實現小型化設計,還能與EFEM系統集成,滿足產線自動化測量需求。運動控制靈活,適配2-12英寸方片和圓片測量。
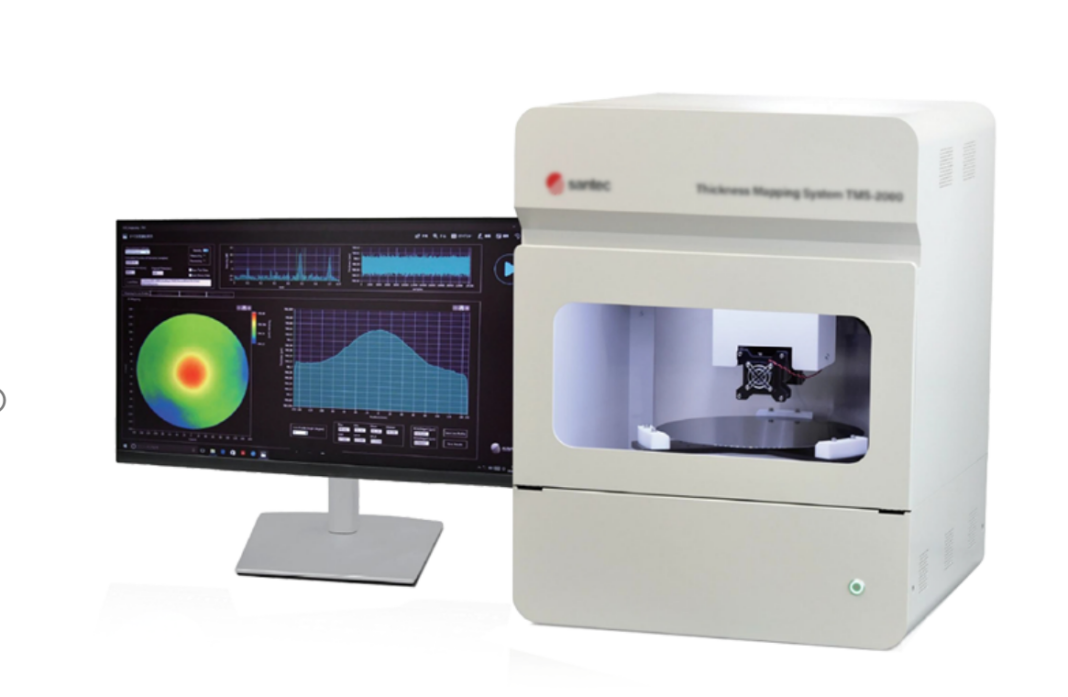
-
晶圓
+關注
關注
53文章
5138瀏覽量
129582 -
機器視
+關注
關注
0文章
3瀏覽量
5440 -
碳化硅
+關注
關注
25文章
3054瀏覽量
50299
發布評論請先 登錄
碳化硅的激光切割技術介紹
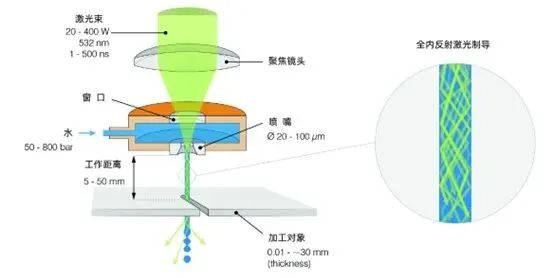
碳化硅深層的特性
淺談硅IGBT與碳化硅MOSFET驅動的區別
碳化硅襯底市場群雄逐鹿 碳化硅襯底制備環節流程
測量探頭的 “溫漂” 問題,都是怎么產生的,以及對于碳化硅襯底厚度測量的影響
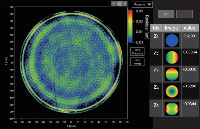
碳化硅襯底 TTV 厚度測量儀器的選型指南與應用場景分析
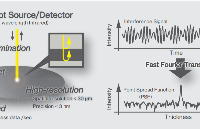
碳化硅襯底切割進給量與磨粒磨損狀態的協同調控模型
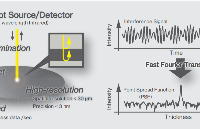
評論