文章來源:晶格半導體
原文作者:晶格半導體
在半導體硅片生產過程中,精確調控材料的電阻率是實現器件功能的關鍵,而原位摻雜、擴散和離子注入正是達成這一目標的核心技術手段。下面將從專業視角詳細解析這三種技術的工藝過程與本質區別。
原位摻雜:生長與摻雜同步的高效技術
原位摻雜堪稱半導體材料摻雜的前沿高效方案,其核心在于將摻雜過程與材料生長過程合二為一。在高溫生長環境下,雜質原子能夠自然融入晶體結構,這一過程不僅不會對晶體結構造成損傷,還能同步激活雜質原子,從而巧妙規避了后續退火工藝及大量熱預算的投入。不過,該技術對材料形態有一定要求,更適用于完整覆蓋的薄膜材料制備。
在實際工藝中,硅烷(SiH?)憑借其優良的反應活性,成為最常用的反應氣體,二氯甲硅烷(SiH?Cl?)和四氯化硅(SiCl?)也偶有應用。當反應氣體抵達硅片表面時,硅烷會發生分解,釋放出硅原子與氫氣。在化學氣相淀積(CVD)過程中,通過精準控制向反應物質流中引入合適的雜質源氣體,即可實現多晶硅生長過程中的原位摻雜。其中,三氯氧化磷(POCl?)作為液態材料,借助惰性氣體以蒸氣形式引入反應裝置,成為 CVD 系統中理想的磷雜質源;乙硼烷(B?H?)、砷化三氫(AsH?)和磷化氫(PH?)等氣態材料,則分別作為硼、砷、磷雜質源參與反應。為確保工藝安全,雜質氣源通常會用氮氣等惰性氣體進行稀釋,一般雜質流占硅烷的比例僅為百分之幾,例如將 PH?稀釋至 2%。
擴散:基于熱運動的傳統摻雜工藝
擴散工藝在半導體和微機電系統(MEMS)技術中占據重要地位,主要用于實現薄膜整體摻雜或局部摻雜區的構建。該工藝的原理基于高溫條件下,雜質原子從高濃度區域向低濃度區域的熱擴散現象,在硅材料工藝中,溫度通常需高于 900°C。
早期半導體技術中,氣相擴散應用廣泛,但因其需使用磷化氫、乙硼烷、POCl?、BCl?等有毒氣體,如今已逐漸被替代。而固相擴散技術成為主流,它利用在待摻雜襯底上預先制備的薄膜材料作為雜質源,這些薄膜多為含硼或磷的玻璃材料。含磷或含硼的玻璃薄膜一般通過低壓化學氣相淀積(LPCVD)設備制備,以低壓硅烷為基礎,混入少量 PH?或 B?H?,在約 400°C、300mTorr 的條件下完成淀積。考慮到高雜質濃度玻璃易吸濕的特性,此類玻璃中的雜質含量通常控制在 4 - 7wt%。
在硅器件平面工藝中,“兩步擴散” 工藝被普遍采用。第一步為恒定表面源擴散,也稱為 “預淀積”。在較低溫度和較短時間條件下,雜質原子在硅片表面形成極淺的擴散層,近似于表面淀積;第二步是將預淀積后的硅片轉移至另一擴散爐,通過高溫加熱使雜質進一步向硅片內部擴散并重新分布,實現所需的表面濃度和擴散深度,此步驟即有限表面源擴散,也叫 “再分布” 。
離子注入:高能粒子操控的精準摻雜技術
離子注入是一種通過將高能離子束注入半導體襯底材料實現摻雜的先進工藝,相比傳統高溫擴散工藝,具有顯著優勢。由于該工藝無需掩膜承受高溫,因此可選用的掩膜材料更為多樣。不過,離子注入過程會對半導體晶格結構造成損傷,需后續通過熱退火工藝修復晶格,并激活雜質原子。
離子注入與擴散工藝的顯著區別在于雜質分布特性。擴散工藝中,因雜質直接與表面接觸,最高雜質濃度位于材料表面;而離子注入能夠精準地將雜質原子注入襯底表面以下,特別適用于制備如埋溝器件等特殊結構。只要離子能量足夠高,還可穿透表面結構,實現深層摻雜。此外,離子注入在雜質濃度和分布控制方面展現出極高的靈活性和精準度,這是傳統擴散工藝難以企及的。
三種技術的綜合對比
從工藝原理來看,原位摻雜是生長與摻雜并行,利用氣相反應實現;擴散依賴熱驅動下的濃度差擴散;離子注入則借助高能離子束的物理轟擊。在工藝條件上,原位摻雜在材料生長溫度下進行,擴散需高溫(>900°C),離子注入雖對溫度要求不高,但后續退火仍需高溫處理。雜質分布方面,原位摻雜和擴散的雜質濃度峰值在表面,離子注入可靈活調控雜質分布深度。從工藝優勢分析,原位摻雜高效節能,擴散工藝成熟、成本較低,離子注入則具備高精度和強靈活性。
-
半導體
+關注
關注
335文章
28803瀏覽量
235805 -
硅片
+關注
關注
13文章
381瀏覽量
35112 -
離子注入
+關注
關注
5文章
35瀏覽量
10497
原文標題:硅片摻雜的幾種方式
文章出處:【微信號:bdtdsj,微信公眾號:中科院半導體所】歡迎添加關注!文章轉載請注明出處。
發布評論請先 登錄
半導體器件生產中的靜電
半導體生產中的靜電問題
SPC在半導體在半導體晶圓廠的實際應用
關于PCB 生產過程中銅面防氧化的一些探討
熒光燈生產過程中的排氣問題
半導體生產過程中的主要設備匯總
在日常生產過程中如何利用測徑儀來對線纜進行測量
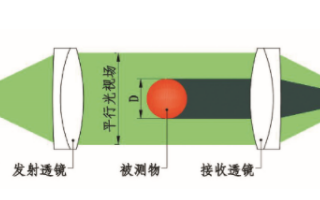
錫膏生產過程中應注意哪些要點?
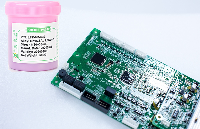
評論