在汽車零部件制造領域,設備作為生產核心要素,其管理水平直接關乎產品質量、生產效率與企業(yè)競爭力。當前,行業(yè)正面臨設備類型多元復雜、運維效率低下、合規(guī)要求嚴苛等挑戰(zhàn),而數字化轉型已成為突破瓶頸的關鍵路徑。本文將結合汽車零部件行業(yè)特性,深度剖析設備資產管理痛點,并基于中設智控在多行業(yè)實踐經驗,探索適配于汽車零部件企業(yè)的智能化管理方案,為行業(yè)數字化升級提供參考。
一、汽車零部件行業(yè)設備資產管理特性與挑戰(zhàn)
(一)行業(yè)設備管理的核心特性
汽車零部件生產涵蓋沖壓、焊接、涂裝、總裝等多道工序,設備類型呈現 “三多” 特征:
- 精密設備多:如沖壓模具、焊接機器人、涂裝生產線等,精度要求達 0.01mm 級,設備故障直接影響零部件尺寸公差與裝配性能;
- 聯動設備多:一條生產線常涉及數十臺設備聯動作業(yè),某一環(huán)節(jié)停機可能導致整條產線癱瘓;
- 特種設備多:熱處理爐、壓力容器、危化品輸送管道等,需嚴格遵循安全規(guī)范,管理疏漏易引發(fā)安全事故。
同時,行業(yè)需滿足 IATF 16949 質量管理體系要求,設備維護記錄、校準周期、性能驗證等需全程可追溯,對管理精細化程度提出極高要求。
(二)現存管理痛點深度解析
- 權屬與流程混亂,效率低下
- 設備采購、使用、維護分屬不同部門,常出現 “采購不問生產需求,維護不知設備狀態(tài)” 的割裂局面。某汽車線束企業(yè)曾因設備選型與工藝不匹配,導致生產線投產半年內停機整改 3 次,直接損失超 200 萬元。
- 故障響應滯后,停機損失巨大
- 傳統人工巡檢難以實時捕捉設備隱患,據統計,汽車零部件企業(yè)平均故障處理時間達 4.2 小時,單條產線每小時停機損失約 8 - 12 萬元。某變速箱生產企業(yè)因軸承磨損未及時發(fā)現,導致齒輪箱報廢,連帶產線停產 12 小時,損失超百萬元。
- 備件管理粗放,成本高企
- 備件分類模糊、編碼不統一,“找件難、庫存亂” 現象普遍。某底盤部件企業(yè)曾出現價值 5 萬元的進口傳感器因庫存積壓過期報廢,而常用密封圈卻頻繁缺貨,年備件資金周轉率不足 3 次,遠低于行業(yè)平均水平。
- 數據孤島嚴重,決策缺依據
- 設備運行數據、維修記錄、能耗數據分散在不同系統,管理層難以獲取實時運營全貌。某企業(yè)因缺乏設備效率分析,盲目增加產線導致產能過剩,設備利用率反從 70% 降至 55%。
二、設備資產管理系統的技術架構與核心功能
(一)智能化管理系統的技術底座
融合物聯網、大數據、數字孿生等技術,構建 “感知 - 分析 - 決策 - 執(zhí)行” 閉環(huán):
- 物聯感知層:通過 PLC、傳感器實時采集設備振動、溫度、能耗等參數,某發(fā)動機零部件企業(yè)部署 300 + 傳感器后,設備異常識別率提升至 92%;
- 數據中臺層:整合設備臺賬、維修工單、備件庫存等數據,形成統一資產數據庫,支持秒級檢索與多維分析;
- 應用層:基于 AI 算法實現故障預測、維護計劃優(yōu)化,如通過振動頻譜分析提前 72 小時預警軸承故障,準確率達 89%。
(二)全生命周期管理功能模塊
- 設備臺賬與動態(tài)管理
- 建立設備 “數字身份證”,記錄從采購(技術參數、供應商)、安裝(調試報告)、運行(保養(yǎng)記錄)到報廢(殘值評估)的全流程信息。某車橋企業(yè)通過電子化臺賬,將設備檔案查詢時間從 30 分鐘縮短至 3 分鐘。
- 智能維護與故障管理
- 預測性維護:基于歷史數據建立設備健康模型,如涂裝線烘箱溫度波動超過閾值時自動觸發(fā)預警;
- 工單閉環(huán)管理:故障申報、派工、驗收全流程線上化,某內飾件企業(yè)實施后,維修響應時間縮短 40%;
- 備件智能管控
- 結合設備運行數據與維修歷史,通過 MRP 算法自動生成采購計劃。某濾清器企業(yè)應用后,備件庫存成本降低 25%,緊急采購次數減少 60%。
- 合規(guī)與績效看板
- 自動生成 IATF 16949 要求的設備校準報告、維護記錄,同時可視化展示 OEE(設備綜合效率)、MTBF(平均故障間隔時間)等核心指標,為管理決策提供數據支撐。
三、行業(yè)實踐案例:從痛點破解到價值落地
(一)某汽車電子企業(yè):數字化轉型的降本增效樣本
該企業(yè)主要生產車載控制器,設備包括 SMT 貼片線、波峰焊設備等精密儀器,原管理模式存在三大痛點:
- 貼片頭損耗率高,年更換成本超 150 萬元;
- 產線切換品種時設備調試時間長,浪費產能;
- 備件庫存積壓與缺貨并存。
解決方案:
- 部署智能監(jiān)測系統,對貼片頭壓力、溫度實時監(jiān)控,結合 AI 算法優(yōu)化焊接參數,損耗率下降 40%;
- 建立工藝參數庫,產線切換時自動調取最優(yōu)配置,調試時間從 2 小時縮短至 30 分鐘;
- 實施備件 ABC 分類管理,高頻使用件設置安全庫存預警,庫存周轉率提升至 5 次 / 年。
成效:年節(jié)約成本約 320 萬元,產能提升 18%,產品不良率從 0.8% 降至 0.3%。
(二)某底盤部件制造商:全流程協同的管理革新
該企業(yè)擁有沖壓、鍛造、機加工等多車間,設備管理面臨跨部門協同難、數據不互通問題。引入設備資產管理系統后:
- 流程重塑:統一設備采購、驗收、維修流程,通過 OA 系統與 ERP 集成,采購審批周期從 15 天縮短至 5 天;
- 移動運維:維修人員通過 PDA 掃碼報修、領取備件,現場處理效率提升 50%;
- 能源管理:監(jiān)測空壓機、熱處理爐等耗能設備,優(yōu)化運行時段,年耗電量下降 12%。
價值呈現:設備綜合效率(OEE)從 65% 提升至 82%,年度運維成本降低 280 萬元,獲評行業(yè) “智能制造示范企業(yè)”。
四、未來趨勢:智能化管理的進階方向
(一)數字孿生驅動的虛實融合管理
構建產線數字孿生體,實時映射物理設備狀態(tài),通過仿真預測設備在不同工況下的性能表現,如某車企利用數字孿生優(yōu)化沖壓模具壓力參數,模具壽命延長 30%。
(二)AI 大模型賦能的智能決策
引入大語言模型分析設備故障知識庫,自動生成維修方案建議,某發(fā)動機企業(yè)試點顯示,復雜故障處理時間縮短 35%。
(三)低碳化與設備管理融合
結合碳足跡核算需求,系統自動統計設備能耗與碳排放數據,為企業(yè)綠色制造認證提供支撐,助力達成 “雙碳” 目標。
在汽車零部件行業(yè)加速向 “智能制造” 轉型的當下,設備資產管理已從傳統運維向 “數據驅動的價值管理” 升級。通過智能化系統的深度應用,企業(yè)不僅能破解設備故障率高、成本失控等現實難題,更能以設備為支點,撬動生產效率、產品質量與管理水平的全面提升。未來,隨著技術的持續(xù)迭代,設備資產管理將成為汽車零部件企業(yè)構建核心競爭力的關鍵抓手,推動行業(yè)向高質量發(fā)展邁進。
-
管理
+關注
關注
2文章
387瀏覽量
26680 -
汽車零部件
+關注
關注
0文章
339瀏覽量
17655 -
智能制造
+關注
關注
48文章
5878瀏覽量
77746
發(fā)布評論請先 登錄
汽車零部件開發(fā)項目管理
機器人零部件企業(yè)智造破局,德沃克OBF智能工廠創(chuàng)新賦能
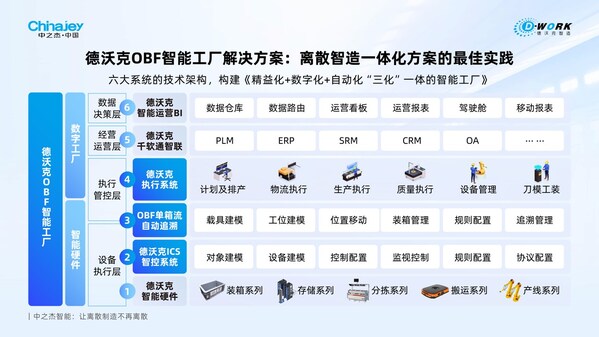
蔡司設備升級助力汽車零部件生產商精準測量車燈
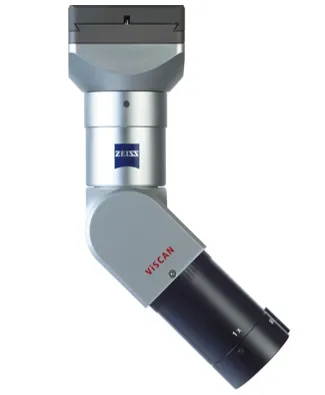
智能零部件管理助力中電思儀的標準化管理
AIM有限公司有效控制零部件的野蠻增長并優(yōu)化企業(yè)流程
麥格納榮獲2024中國汽車及零部件行業(yè)發(fā)展創(chuàng)新大獎
3D 視覺定位技術:汽車零部件制造的智能變革引擎
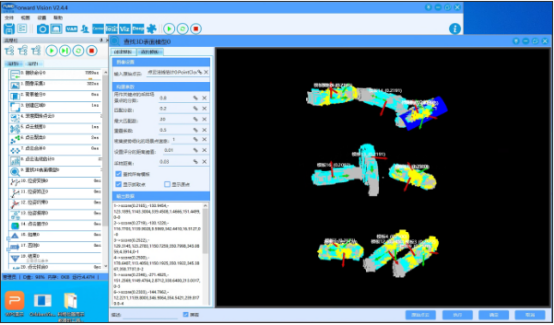
三品PLM系統在汽車零部件行業(yè)的解決方案及應用
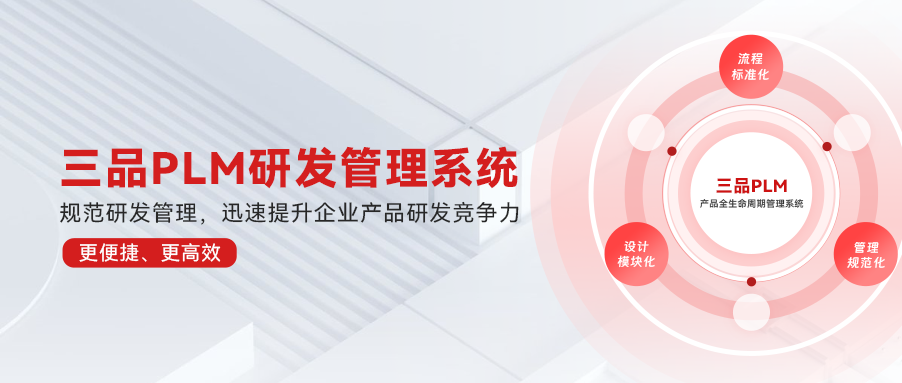
評論